An open AI platform for all service processes: That is the goal of Service-Meister. In order to develop AI functions, the project relies on six speedboat projects that not only solve challenges in industrial service, but also provide answers to urgent questions about climate change.
The KROHNE / inovex speedboat project
Keeping an eye on water levels from a distance, determining discharge rates, and identifying problems
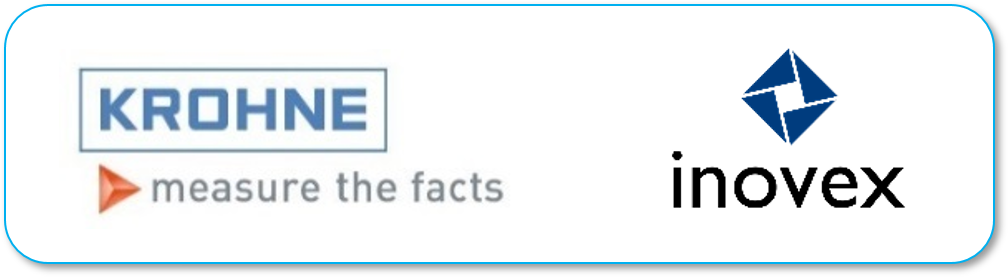
As an expert in process instrumentation and automation, KROHNE works closely with customers from different sectors and industries. In order to be able to react to unforeseen events in a timely and appropriate manner, smart real-time monitoring is needed that allows our customers to reliably keep an eye on their processes, even remotely. KROHNE makes this possible by means of a comprehensive portfolio of Internet-of-Things-capable sensors, as well as a corresponding IoT platform. This IoT solution is being further developed in Service-Meister together with the IT project house inovex smart.
To this end, KROHNE and inovex are forming one of six fast boats. Both partners want to realize AI functions in their use case and offer them to all users of KROHNE’s platform. The new modules will, for example, visualize sensor data using AI methods, predict malfunctions and optimize deployment planning. The result: smarter management systems for all users of the IoT platform.
About the two companies:
inovex is an innovation-driven and quality-driven IT project house with a focus on Digital Transformation. More than 350 IT experts support companies comprehensively in the digitalization and agilization of their core business and in the realization of new digital use cases.
KROHNE is your reliable partner for process instrumentation and automation. As our client, you benefit from our ability to find the right measurement solutions for your applications. We offer a complete product portfolio, industry-specific system solutions, and complementary services.
The WÜRTH / grandcentrix speed boat project
Accelerate service processes, detect faults remotely
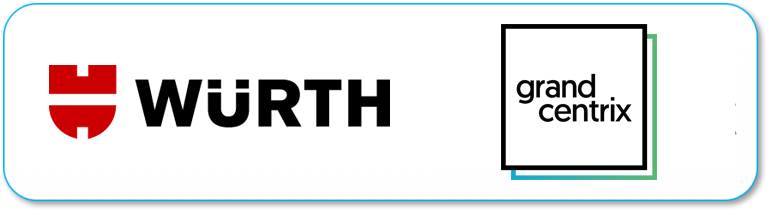
Innovations for the individual, which later benefit the general public – that is the idea of Service-Meister. And also the idea in the use case from assembly expert WÜRTH and system house grandcentrix. WÜRTH’s new power tools, first released in 2019, comprise tools which are networked for the first time and can therefore collect and transmit data. This is information that can be analyzed in order to accelerate service processes and to detect faults remotely. The use case therefore focuses on predictive maintenance. And on data from the service organization itself: Whether by telephone, email, or website – AI procedures analyze the devices’ service reports and IoT data. If incidents and service requests can be related to each other, this improves service quality and also creates new opportunities for self-service.
About the two companies:
Würth is the world market leader in the sale of assembly and fastening materials. The Würth Group currently consists of over 400 companies in more than 80 countries and has over 77,000 employees on its payroll. In the business year 2018, the Würth Group achieved sales of EUR 13.6 billion.
grandcentrix is the quality leading IoT solution provider for Smart Products, Internet of Things, Smart Home, and Smart Energy. With its more than 150 employees at its locations in Cologne and Dortmund, grandcentrix covers the complete technology and user experience expertise for future-proof large-scale IoT production.
The Open Grid Europe / USU speed boat project
Detect anomalies, forecast service requirements
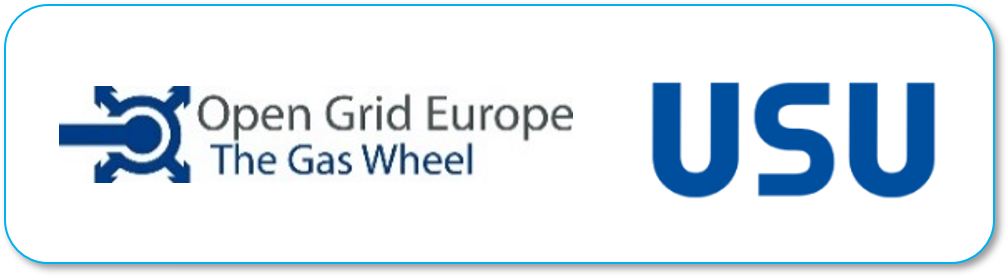
Classify problems automatically and solve them remotely: Open Grid Europe transports natural gas through its 12,000-kilometer long pipeline network. The network operator is obliged to remotely monitor its power plant identification systems in a quality-assured manner. To this end, Open Grid Europe operates its own Competence Center, which is tasked with detecting anomalies in the data streams of all 850 or so sensors. Together with USU Software, the largest European provider of IT and knowledge management software, Open Grid Europe wants to further develop its monitoring with AI. The goal: to improve service knowledge management, automatically detect anomalies, and forecast maintenance requirements. In addition, technicians will use AI-based chatbots to solve complex problems.
About the two companies:
OGE – Open Grid Europe GmbH (E.ON Gastransport GmbH until August 2010) is a transmission system operator for natural gas based in Essen. OGE operates Germany’s largest pipeline network with a length of around 12,000 km, including through its shareholdings in the MEGAL, TENP, NETRA, and DEUDAN pipelines. OGE is part of the NetConnect Germany market area.
The USU Group is the largest European provider of IT and enterprise service management solutions. USU is the only company on the market to offer ready-to-use solutions for all areas of technical service.
The Trumpf / USU speedboat project
Diagnose problems automatically, reduce maintenance costs
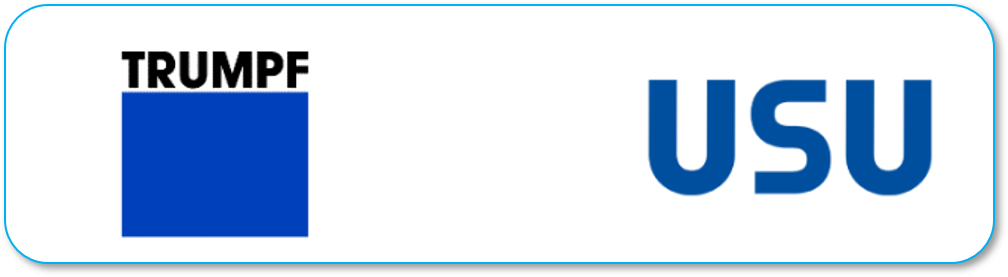
Efficient planning of service calls, automatic diagnosis of machine data – these are the goals in the speedboat project from TRUMPF and USU Software. After all, TRUMPF machine tools are complex, and operating and maintenance costs influence buyers’ decisions. The solution provides the right combination of sensor technology, diagnostic procedures, and AI know-how. The machines should be able to independently diagnose and analyze problems in order to transfer results to a cloud platform where they can be evaluated in a differentiated manner. The result: maintenance tickets can be automated and information can be used in a continuous learning and improvement process. This increases system availability and reduces maintenance costs.
About Trumpf
Trumpf. To further develop production technology, to make it economical, precise, future-proof, and networked – that is our task. We are the market and technology leader in machine tools and lasers for industrial production and our innovations can be found in almost every industry.
The Atlas Copco / USU speedboat project
Increase quality, keep equipment available
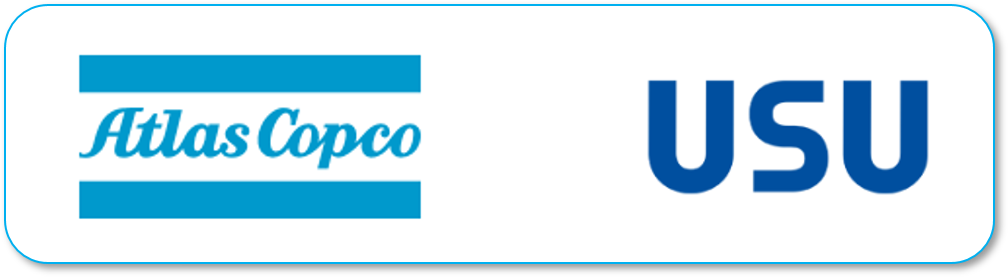
Monitoring production processes, preventing downtime – Atlas Copco glues and joins, for example, to connect cables for its compressors. If there are problems in production, things come to a standstill in more in one factory. Downtimes threaten the entire supplier network and the quality of all products. To reduce waste and keep equipment available, Atlas Copco relies on AI. Together with USU Software, Atlas Copco is working on a service knowledge management system that monitors gluing and joining processes with AI to detect production errors and deviations during operation. To ensure that the system automatically alerts technicians in the factories, numerous data and sensor sources must be integrated. Ultimately, the AI should be able to identify errors independently and also access historical data from service calls. The advantage: causes can be determined more precisely.
About Atlas Copco
Atlas Copco has been present in Germany for over 60 years. The company started on 21March 1952 as Atlas Diesel GmbH in Essen-Kupferdreh with four employees. The German sales company in Essen was the first foreign branch of the Swedish group. Today Atlas Copco is present in over 180 countries.
The KEB / USU speedboat project
Planning field operations, procuring spare parts
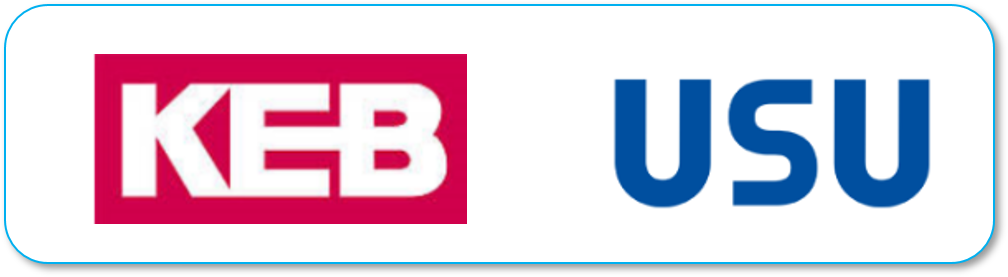
Collecting service data efficiently, evaluating it automatically in real time and making it available contextually – the use case from drive expert KEB and USU Software relies on an extensive pool of information. The speedboat project not only processes data from sales, service and customer communications, but also error descriptions and live events such as alarm messages and machine statuses. Whether video, augmented reality or chatbot – results of the AI analyses should be able to be integrated into different tools, depending on the service application. This way, technicians should automatically receive support. And recommender engines should help to plan field service assignments and procure spare parts.
About KEB
Since its foundation in 1972, KEB has developed into a globally operating medium-sized company with more than 1,400 employees, more than 900 of whom work at the headquarters in Barntrup in the west of Germany. KEB develops, produces, and sells a wide range of industrial automation technology components with a focus on electrical drive and control technology.